Factory evolution: the plastic injection moulding shop
At the moment VENTS is worldwide acknowledged ventilation leader. The company employs about 2,500 persons and has 16 state-of-the-art production shops – each one enough to build a separate factory around. However, in the mid-90s our company could only dream of today’s scale with a few hundred staff and a modest 3-shop production facility.
Over the course of 15 years VENTS has come a long way evolving from a combination of business units into a community of like-minded individuals. The company’s leading positions are squarely based on the winning combination of developing highly automated production and restless innovation. This article continues the «VENTS: Behind the Scenes» series telling the story behind the founding and evolution of the plastic injection moulding shop (PIMS).
Inception
The plastic injection moulding shop which produces a wide range of components for household fans, ventilation grilles, diffusers and much more rolled out its first batch in early 90s. Back in the days it was manned by a staff of 30 and had only 7 thermoplastic processing machines and a few dozen injection moulds. Over the course of a few years the shop was massively reorganized: the production moved to a much larger facility and received a host of high-tech equipment upgrades which gradually replaced all the obsolete units.
Today the PIMS takes up 4,500 m2 of space and operates 24/7 employing about 230 highly skilled professionals. There are about 100 thermoplastic processing machines which use 10 kinds of raw polymers from leading suppliers worldwide to guarantee the outstanding performance and admirable aesthetics of VENTS products.
The numbers alone speak to the sheer scale of the transformations. However, our main goal is to unfold the mystery of the company’s inner works and provide an insight into what really makes VENTS a ventilation equipment leader.
Harnessing the tricky plastic
The shop runs round the clock seven days a week. All the fabrication steps are automated to the maximum and follow a carefully designed algorithm. The birth of each item begins with raw material preparation, loading the thermoplastic processing machine and then finally removing the ready piece once it has cooled down. Each moulder is in charge of two machines and normally takes care of item processing and machine maintenance operations as well as communication with support functions during the shift. The responsibility for each process is assigned to a dedicated shop floor worker. For example, the moulders are responsible for the quality of fabricated parts while the service engineers promptly fix any malfunctions to minimise downtime and production rejects.
Pride and glory
We have had a chance to discuss the PIMS equipment evolution with Sergey Povkh – the shop manager who has been in charge of the facility for more than 15 years. His guiding principle applied to both work and everyday life is «Think, tell, act and control».
«The capacity utilisation grows every year while our products become more and more complex. This requires a sustainable equipment upgrading policy as well as continuous perfection of our technology processes and professional development of our staff. Our range of equipment currently includes more than 700 pressure moulds and some 100 new-generation thermoplastic processing machines capable of producing parts of various complexity as well as 40 loading machines, high-performance thermostats and chillers. Besides facilitating the tasks at hand these efforts are aimed at speeding up all the processes many-fold and improving the production efficiency and the quality of our finished products».
Sky is the limit
About a year ago the entire VENTS facility including the PIMS actively joined a Lean Production scheme pioneered by Toyota. A dedicated action group identifies all kinds in waste at all steps of the fabrication process, analyses them and makes the appropriate efforts to eliminate them at the origin. Such practice leads to a significant optimisation of the work flow, prevents production rejects, minimises downtime, reduces material waste and ensures a more balanced load of the human resources.
Read more
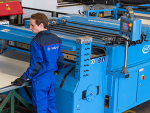
5 Mar 2024
Vents launched a new coil processing line
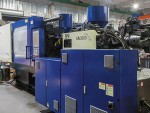
12 Oct 2022
Vents plans to Put Into Operation a Non-standard Injection Molding Machine
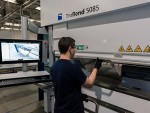
28 Sep 2022
Upgrading the capacities: new machines for metal processing
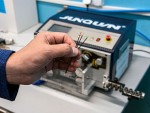
13 Sep 2022
Upgrading the capacities: small machines for complex tasks
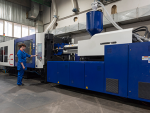
1 Sep 2022
Upgrading the capacities: new capacities for plastic products manufacture
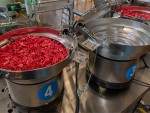
23 Aug 2022
Upgrading the capacities: a new packaging complex has been put into operation
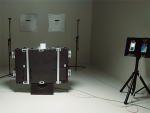
18 Jan 2022
Reverberant chamber for acoustic testing of products was put into operation
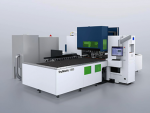
12 Oct 2021
One machine – two technologies
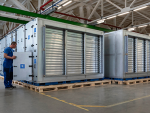
27 Jul 2021
AirVENTS: bigger, higher, more efficient
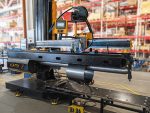
26 May 2021
Vents continues to introduce automation into its welding works
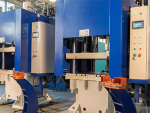
13 Apr 2021
New presses expand opportunities for the metalware workshop
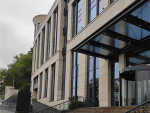
9 Dec 2020
VENTS ventilation equipment ensures fresh air supply in a new business centre
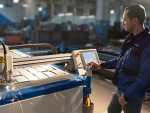
3 Dec 2020
Vents capacities are complemented with a new metal plasma cutting machine
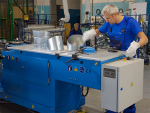
26 Aug 2020
New machine tools for production of shaped products have been put in operation
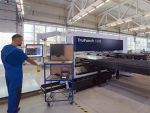
20 Aug 2020
Vents facilities will become stronger due to launching a new TruPunch 1000 machine tool
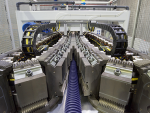
19 May 2020
VENTS enhances its production capacity by adding a new manufacturing line for semi-rigid air ducts
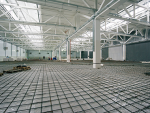
29 Apr 2020
VENTS dedicates 3,500 of floor space to its new project
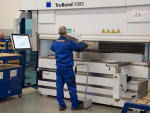
16 Apr 2020
New bending machine TRUMPF is running!
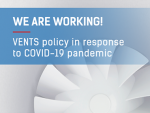
8 Apr 2020
We are working! VENTS policy in response to COVID-19 pandemic
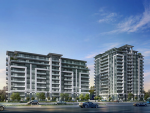
10 Dec 2019
Hundreds of VENTS ventilation units to provide fresh air for Canadian homes
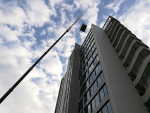
26 Nov 2019
AirVENTS reaches a new height
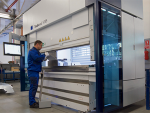
7 Nov 2019
One more engineering marvel in VENTS equipment fleet
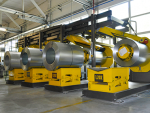
10 Oct 2019
VENTS commissions a one-of-a-kind production line
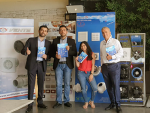
13 Aug 2019
VENTS continues its expansion into Middle Eastern markets
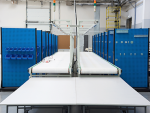
22 Jul 2019
Big company, big plans
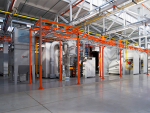
7 May 2019
A new coat of paint for VENTS ventilation products
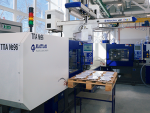
9 Apr 2019
VENTS stays committed to automating its manufacturing processes
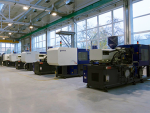
5 Feb 2019
VENTS: from commissioning new machining centres to opening new factory shops
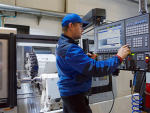
5 Dec 2018
CNC reinforcements from Japan for the tool production unit
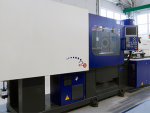
22 Nov 2018
VENTS ramps up production
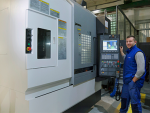
14 Nov 2018
VENTS stays true to facility upgrade plans
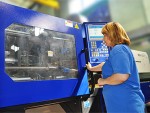
12 Sep 2018
VENTS continues upgrading production facilities

10 Sep 2018
VENTS opens doors to Polish visitors
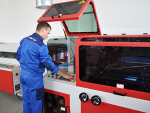
29 Aug 2018
VENTS automates packing
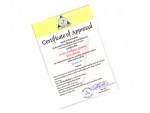
23 Aug 2018
VENTS adopts international standard for quality management systems
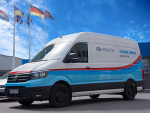
22 Aug 2018
VENTS maintenance service: always at the ready!
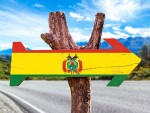
12 Jun 2018
VENTS advances to South America
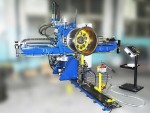
23 Jan 2018
Holiday season addition to VENTS equipment fleet
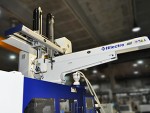
11 Dec 2017
VENTS to commission a servo robot
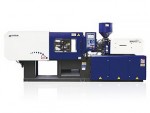
16 Nov 2017
Autumn upgrades for VENTS factory equipment